Profiling - V-Cut scoring
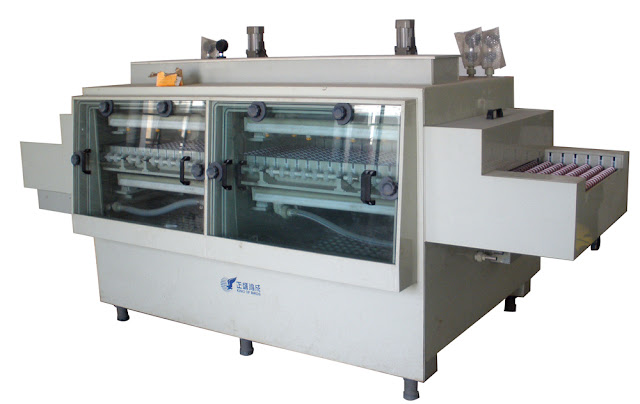
The final manufacturing stage is to profile the PCBs and cut them out of the production panel. For this we use a computer-controlled milling machine or “router”. First the machine mills out any small slots or internal cut-outs. The cutter follows the path defined in the original tool file. Next the milling head automatically picks up a 2 mm cutter, checks the diameter and mills around each PCB. The brush around the milling head ensures that all the dust produced is collected by the vacuum system. The circuits are held in place by small bridges of material. We will drill through these and then remove each separate PCB from the production panel. This panel has also been V-scored.